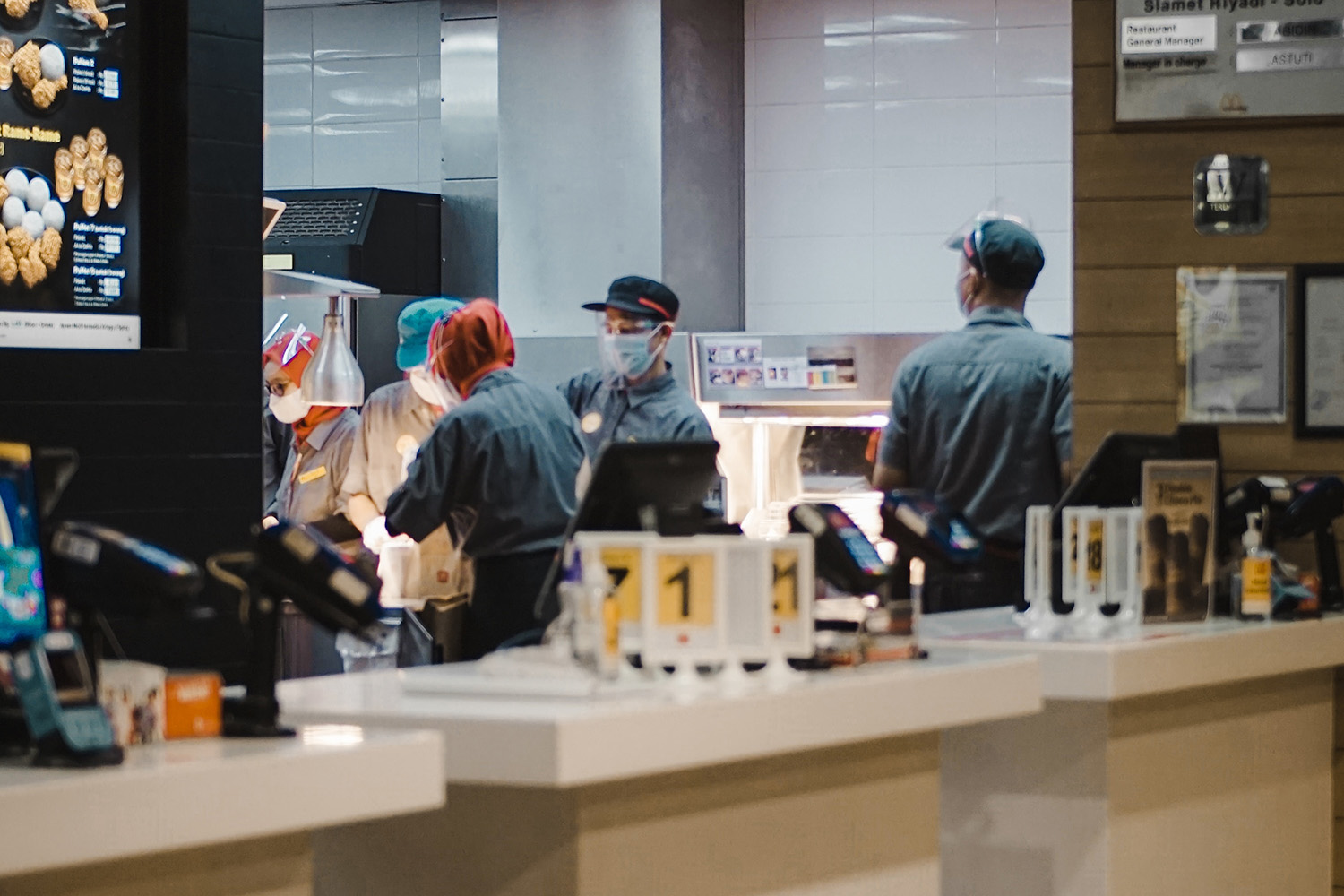
Okappy Lambtrad Case Study
Lambtrad, a holding company which owns 13 McDonalds outlets across Somerset, approached Okappy last year during a big growth period in which it was building three new branches.
Lambtrad was seeking a solution to help better manage the plethora of operational activities and maintenance contracts across all its branches. With more than 150 pieces of equipment in each branch staff were eager to find an effective solution to support their expansion as any inefficiencies would only get amplified as they grow – causing more and more problems.
Why did Lambtrad choose Okappy?
After initial meetings with Okappy founder Richard Harris, it became apparent that although the McDonald’s master franchise does provide a software system, area manager Carl Fielder at Lambtrad felt they needed something that offered more functionality and provided a better quality of service.
Carl said, “When compared to other systems available Okappy was more user- friendly and when asking for information the team were much more engaged with me than others.”
How is Lambtrad using Okappy?
One great benefit to Lambtrad is that Okappy has the functionality for the restaurants and employees to log and prioritise jobs that need doing.
Carl added:“We have a maintenance team we employ to help maintain the catering equipment across our 13 restaurants. The restaurants use Okappy to log any equipment errors or downtime and the engineers react to each job created depending on priority.”
Okappy has an audit log which is useful for the restaurants as staff often get questions from Lambtrad such as why they have not serviced a machine. On the Okappy platform they can see the audit log and see when they placed a call with the result that less time is wasted chasing after updates and everyone is better informed.
It also means Lambtrad can stay on top of what its engineers and subcontractors are doing and can get updates coming in real time, including when an engineer has got to site at the start of a job.
They can even use Okappy to monitor PAT tests and then print off the job sheet as proof of insurance.
As Lambtrad continues on its current growth trajectory, it is looking to utilise the suite of functionality that Okappy offers more. Lambtrad is very keen on the fact that staff can track their vans using the Okappy app or tracking devices and plan to start using this soon. Additionally, they want to use Okappy to monitor and attempt to reduce their energy consumption to take steps to become more sustainable.
Do you find Okappy has streamlined your business and reduced costs? Can you give an example?
The restaurants feel the pain when equipment is down as it leads to lost revenue and customer complaints. Using Okappy has meant a big reduction in downtime caused by faulty equipment.
This is a big saving for them because if a machine such as the milkshake maker goes down, it can cost them thousands of pounds per hour in lost sales.
“For me personally Okappy saves me about four-to-five hours of admin time a week, having to scroll through Google sheets and follow up on engineers with no real idea of what’s completed, when it was fixed, the downtime, etc. Then the engineers themselves find it so useful as they are also more aware of what jobs they have/haven’t completed, what’s awaiting parts, etc and, also the fact they can see all 13 restaurants on the same screen.”